In the fast-paced world of product development, efficiency and speed are paramount. Companies are constantly looking for ways to streamline their processes and bring innovative products to market faster than ever before. One method that has gained significant attention in recent years is rapid injection molding. This technique not only accelerates the manufacturing process but also offers enhanced flexibility and precision, making it an ideal choice for prototyping and low-volume production.
Rapid injection molding allows designers and engineers to create high-quality parts in a fraction of the time traditionally required. By leveraging advanced technologies and materials, it enables rapid turnaround on mold creation and modification, which in turn facilitates quicker iterations and testing. As businesses strive to maintain a competitive edge, understanding and adopting rapid injection molding can be a game-changer, revolutionizing how products are developed and introduced to the market.
Understanding Rapid Injection Molding
Rapid injection molding is a manufacturing process that allows for the quick production of plastic parts through the use of specialized molds and advanced technology. This technique significantly speeds up the development cycle, enabling companies to bring products to market faster than traditional methods. By utilizing prototype-grade materials, rapid injection molding facilitates the testing and validation of design concepts before full-scale production begins.
One of the main advantages of rapid injection molding is its ability to produce high-quality parts with precision and consistency. This process uses computer-aided design and manufacturing technologies to create molds that can be adjusted easily. As a result, engineers can iterate designs swiftly, minimizing the time spent on modifications and ensuring that the end product meets specific performance requirements.
Additionally, rapid injection molding can significantly reduce costs associated with product development. By streamlining the prototyping phase and cutting down on the amount of material waste, manufacturers can save both time and resources. This is particularly beneficial for startups and small businesses looking to innovate without the burden of large upfront investments. As such, rapid injection molding stands as a cornerstone in the future of efficient product development.
Benefits of Rapid Injection Molding
Rapid injection molding offers substantial time savings in the product development process. Traditional molding methods can take weeks or even months for tooling and production setup. In contrast, rapid injection molding significantly reduces this lead time, allowing companies to move from concept to prototype in a matter of days. This speed enables businesses to respond more quickly to market demands and encourages innovation, as ideas can be tested and refined at an accelerated pace.
Cost efficiency is another critical advantage of rapid injection molding. While the initial investment in tooling might seem high, the ability to produce parts quickly and efficiently allows manufacturers to achieve economies of scale sooner. This method minimizes the waste of materials and reduces labor costs, which ultimately leads to lower overall production costs. Companies can also benefit from shorter production runs without incurring exorbitant expenses, making it feasible to develop customized parts in small quantities.
Furthermore, rapid injection molding achieves high precision and quality in the manufactured parts. The technology allows for intricate designs and complex geometries that are difficult to achieve with traditional processing methods. The consistency in production ensures that the final products meet stringent quality standards, which is essential for industries such as automotive and medical devices. This reliability reinforces customer confidence in the manufactured goods and supports long-term business relationships.
Future Trends in Product Development
As industries evolve, the demand for quicker turnaround times and cost-effective solutions in product development continues to grow. Rapid injection molding stands out as a pivotal technology that enables manufacturers to streamline their processes. With advancements in materials and machinery, companies are finding innovative ways to reduce lead times significantly. This not only accelerates the production cycles but also allows for more frequent updates and iterations of product designs, catering to consumer preferences with agility.
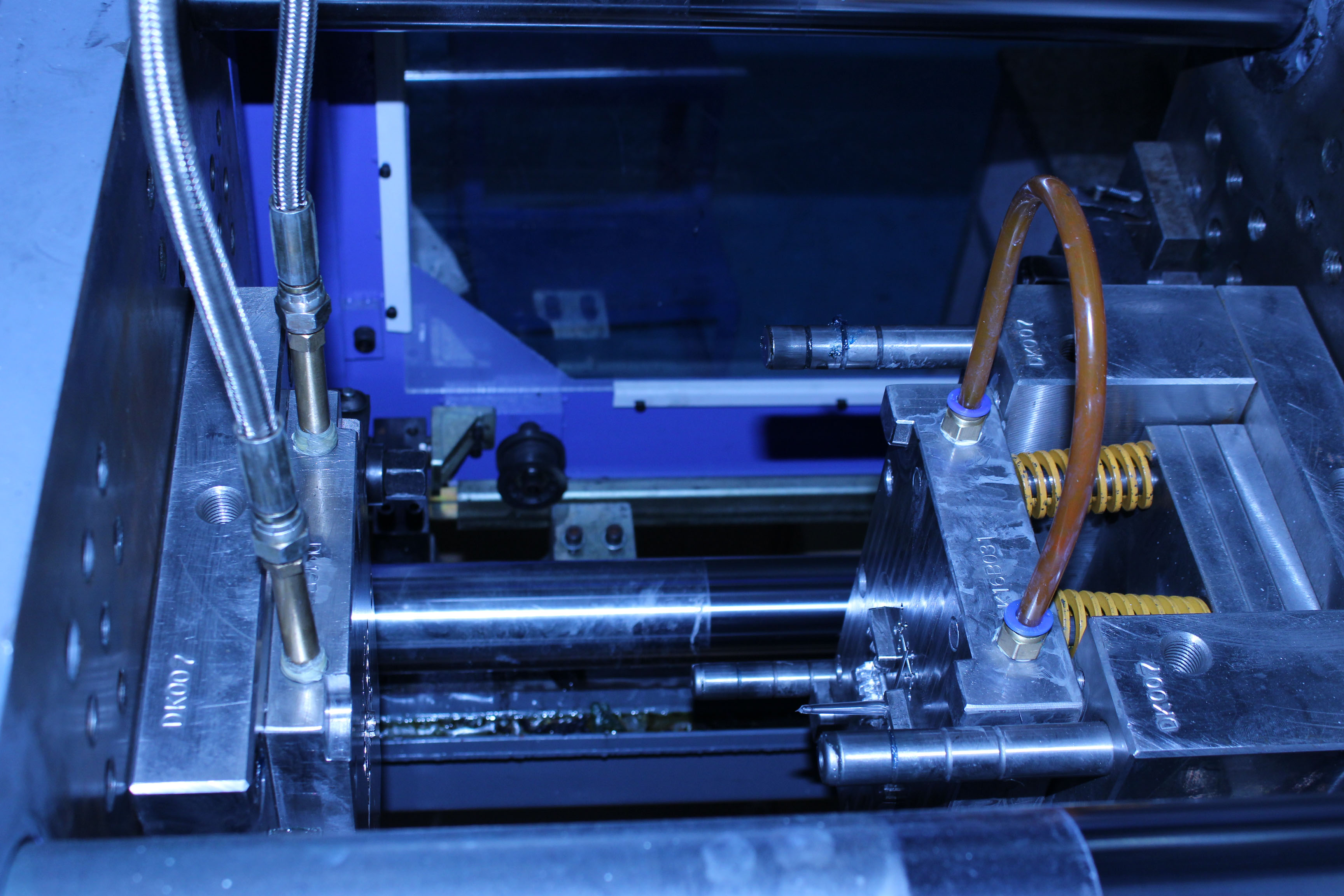
Another trend shaping the future of product development is the integration of digital technologies, such as 3D printing and simulation software. These tools complement rapid injection molding by facilitating the creation of prototypes that can be tested and modified before final production. This seamless combination enables designers and engineers to visualize and validate their concepts rapidly, minimizing costly mistakes and enhancing the overall quality of the final products. The synergy between these technologies marks a transformative shift in how products are brought to market.
Sustainability is becoming a central theme in product development, and rapid injection molding is adapting to meet these environmental considerations. The industry is witnessing a growing emphasis on using recycled materials and energy-efficient processes. As companies become more environmentally conscious, they are seeking solutions that not only meet consumer demand but also align with their sustainability goals. This trend indicates a future where rapid injection molding plays a key role in creating eco-friendly products while maintaining efficiency and innovation in manufacturing.